【第3章】第2節 設備、作業等の具体的な改善の方法
第2節 設備、作業等の具体的な改善の方法
(1)5つのステップと基準
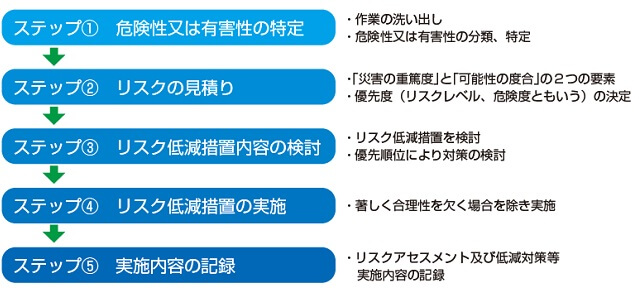
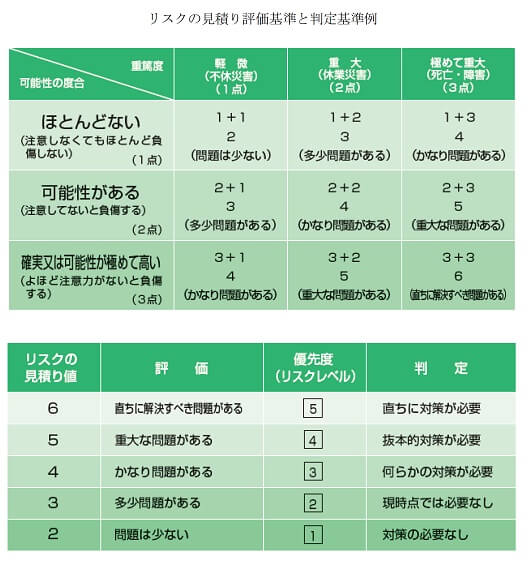
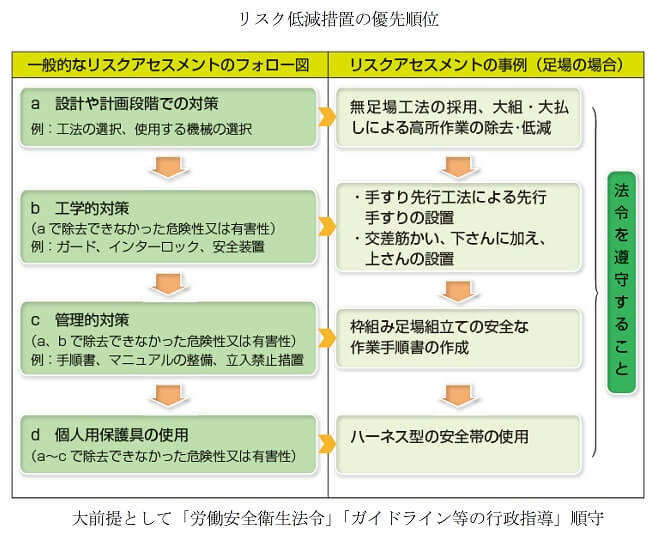
a:危ない機械設備は使用しない、危ない原材料は使用しない、危ない作業はしない
b:危ない箇所には覆いや囲いを設ける、安全装置や局所排気装置を設ける
c:人の行動に制限をかける、教育訓練、法令以上の立ち入り禁止措置を行う
d:最終手段、あるいは念のために個人用保護具を使用させる
※リスクレベル(優先度)に合わせた改善対策が必要です。
(2)効果
安全衛生の確保は「機械、設備、もの」に頼る本質安全化となります。
また、十分にリスクを低減化できなかった問題点は、毎日の危険予知活動の中で「行動面」から対応していくことになります。
(3)実施についての問題点
リスク低減措置は「時間」と「費用」を必要としますので、経営者は労働災害防止意識と対策費用の捻出に苦労することになります。「人間尊重の理念」を深く経営者は持って、出来るところまでは取り組んでいただきたいと思います。
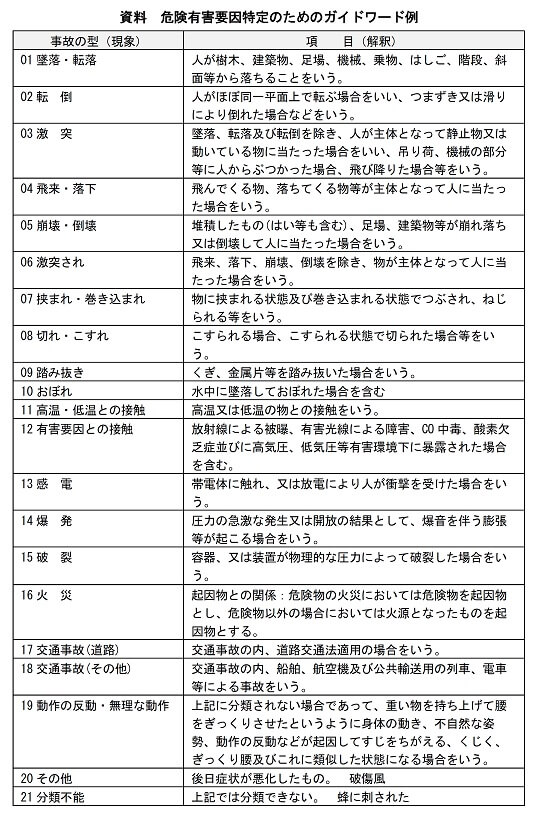
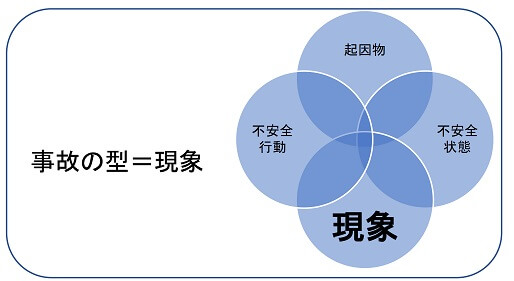
不要材が散乱していると「不安全な状態」
脚立を作業位置に近づけておけないので「不安全な状態」
手が届かなくなるので「不安全な状態」
手をいっぱいに横に伸ばすと「不安全な行動」
脚立から(起因物)
➡ 墜落する(あるいは落ちる)
(事故の型→現象)
■管理に欠陥があると「不安全状態」「不安全行動」が発生しやすくなる
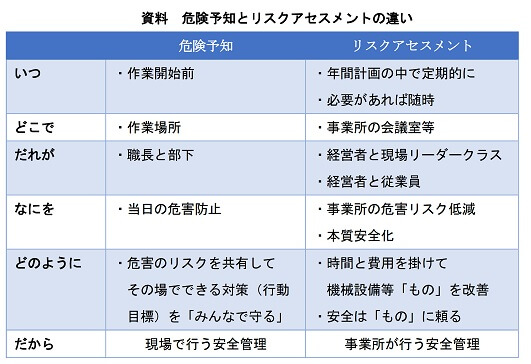
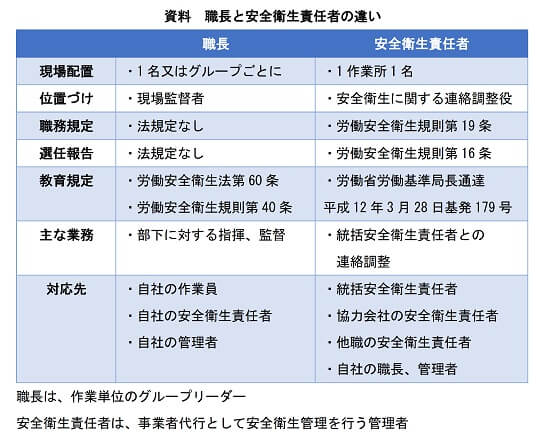
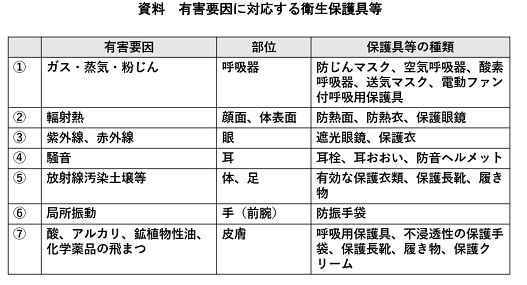
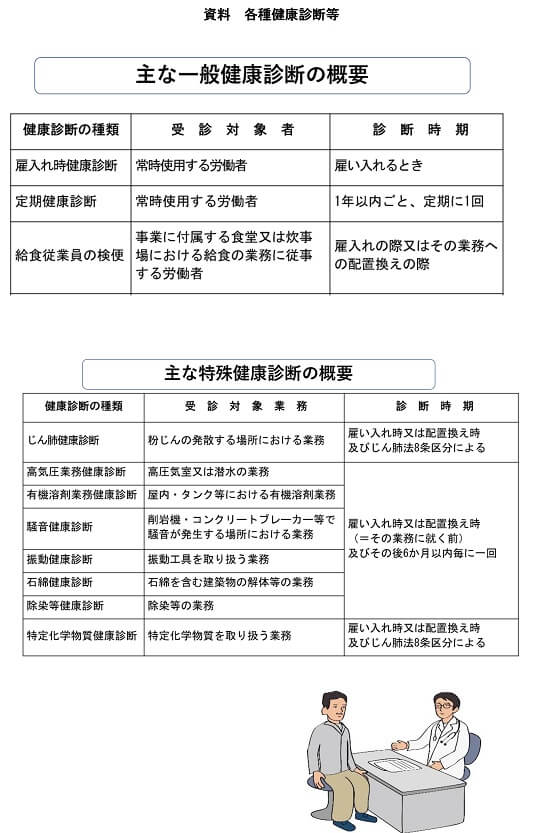
地域・講習・人数に合わせてすぐに予約可能
講習会を予約する受講者様のご希望に合わせ、以下のタイプの講習会もご用意しています

一般講習
全国の都道府県で定期的に開催

WEB講習
オンラインで会社や自宅で受講可能

出張講習
指定の会場へ講師を派遣いたします

このページをシェアする
講習会をお探しですか?