リスクアセスメントの進め方、書き方、そして事例まで
リスクアセスメントとは、職場における危険性又は有害性等の調査のことで、その結果に基づいて対策を実施していく一連の手法のことでもあります。
労働災害の原因となるような危険性又は有害性等を調べて特定し、そのリスクを見積り、見積もったリスクの除去・低減措置を検討し、低減効果の高いものなどの優先順位をつけて対策を実施していきます。
リスクアセスメントの進め方については、厚生労働省から「危険性又は有害性等の調査等に関する指針」が公表されています。
こうしたリスクアセスメントの実施は、いまや事業者の努力義務(労働安全衛生法第28条)となっていますので、職場での「リスクの低減」に向けて、リスクアセスメントに積極的に取り組みましょう。
「リスクアセスメントには、手法があります」
こちらのページでは、リスクアセスメントを進める為に必要な『5つのステップ』を紹介いたします。
5つのステップを順次実施して、この手法をしっかりと身に付けましょう。
目 次
◆ 最初に、リスクアセスメントのキーワードを理解しよう。
◆ リスクアセスメントは、なぜ必要なのでしょうか。
・なぜリスクアセスメント?① ~イギリスの取り組みと5ステップ方式~
◆ リスクアセスメントには、手法があります。
◆ 実際に、リスクアセスメントを実施してみましょう。
◆ リスクアセスメントの歴史を見てみよう。
◆ リスクアセスメントを進める上で確認しておきたいページです。
執筆者:労働安全コンサルタント 中井知章
◆ 最初に、リスクアセスメントのキーワードを理解しよう。
昨今、事故災害の未然防止の方法として、リスクアセスメントの手法が広く導入され実施されています。リスクアセスメントとは、一言でいえばリスクの事前評価のことです。
それでは、リスクとは何でしょうか。また安全とは何でしょうか。リスクアセスメントを実施するために必要なキーワードを理解することから始めましょう。
リスクとは
「リスク」という言葉を最近よく耳にしますが、難しい定義を知らなくても私たちは感覚的にその意味を知っています。例えば、どこの家庭にもある「包丁」ですが、これは「リスク」があるでしょうか?それとも無いでしょうか?と問われれば、たいていの人は「ある」と答えるのではないでしょうか。
同様に、「野球」や「バレーボール」といったスポーツ、「駆け足」や「階段の上り下り」といった動作、「電車」や「自動車」といった乗り物、「飴玉」や「餅」などの食品・・・様々な物・場合について考えてみると、私たちの身の回りには無数の「リスク」が存在していることがわかります。私たちは「リスク」と付き合いながら生活している、と言ってもよいかもしれません。
さて、「リスク」とはいったい何なのでしょうか?
辞書やインターネットの記事で調べてみますと、以下のような説明がされています。
- 「危険」や「危機」
- 危険の生じる可能性
- 危険度
- 将来いずれかの時に起こる不確定な事象とその影響
- 何か悪い事が起こる可能性
どうもひとことで言い切れるようなものでもないようですが、ここでは「リスク」とは、「人にとって良くないことが起こる確率と、起こった時の危害の程度の組み合わせ」と定義付けたいと思います。
(※良し悪しに関わらず、「発生が不確実な事象」全般を指す考え方もあります)
例えば、「包丁」について考えてみますと、「良くないこと」とは「誤って手を切ってしまう」ことが考えられますが、そのことの「起こる確率」と「危害の程度(この場合はけがの程度)」は、「ごくまれに(比較的軽い)切り傷を負う」といったことになるでしょう。従って、「決して無害とは言えない」ということで「リスクがある」と判定するわけです。
さらにこのことを労働災害に置き換えて考えてみますと、
「人にとって良くないことが起こる確率」→「仕事の上で負傷又は疾病が発生する可能性」
「人にとって良くないことの程度」→「発生した時の負傷又は疾病の程度(重篤度)」
であり、下図の四角の面積が「リスクの大きさ」を示しています。
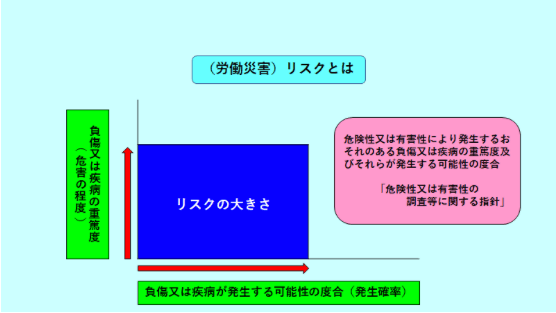
※なお、厚生労働省が平成18年(2006年)に示した「危険性又は有害性等の調査等に関する指針」では、リスクとは「危険性又は有害性によって生ずるおそれのある負傷又は疾病の重篤度及び発生する可能性の度合」と規定されています。
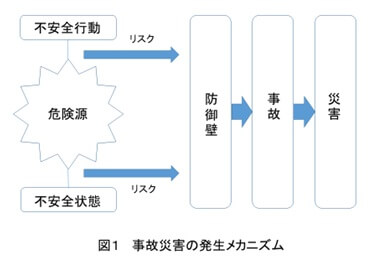
また、事故災害は、危険源(労働災害を引き起こす潜在的根源)が不安全な状態であったり、危険源に人が不安全な行動で接触したりするときに発生します。
事故災害を減らすために、事故災害の発生頻度および重篤度によって、事故災害の発生を防止するために優先順位をつけて対策をたてます。すなわち、事故災害の発生頻度と重篤度の両者を考慮して(組み合わせて)、未然対策をたてることがポイントです。
危険源とリスクの違いとは
危険源とは、労働者に負傷又は疾病を生じさせる潜在的な根源であり、「ハザード」と呼ばれます。労働安全衛生法では、「危険性又は有害性」と表現されています。
リスクは、危険源が不安全な状態であったり、危険源に人が不安全な行動で接触したりするときに発生します。労働安全衛生法では、「危険性又は有害性等」と表現されています。
受け入れ可能なリスクと許容可能なリスクとは
リスクには、「受け入れ可能なリスク」と「許容可能なリスク」があります。
前者の「受け入れ可能なリスク」とは、リスクが顕在化して災害に至っても、かすり傷程度の微傷なリスクで、広く受け入れられるリスクであります。
「受け入れ可能なリスク」にまで、リスクを低減するのが理想ですが、現実は、リスク低減対策には大きなコストがかかること、また便益が損なわれることを考慮して、「広く受け入れ可能なリスク」にまで、リスクを低減しない、すなわち許容してもよいリスクが存在します。
これが後者の「許容可能なリスク」であります。また、「許容可能なリスク」よりも高いリスクの状態を「許容不可能なリスク」といいます。
自動車の運転を考えてみますと、我が国で毎年4000人以上の人が交通事故で死亡しています。労働災害による死亡よりも4倍も多くの人が死亡しています。これは、誰もが受け入れられるような小さなリスクであるとは言えません。しかし、利便性を考えて多くの人が運転しています。これは、自動車を運転することが、「許容可能なリスク」と容認しているからです。
安全とは
「安全」という言葉について考えてみますと、どうもつかみどころがないことに気付きます。
例えば、
- 10年間無事故無違反だったドライバーが「安全運転」しかしなかったのか?
- 1年間無事故の建設現場は「安全」なのか?
- ケガが発生していないことが「安全」と言えるのか?
よく考えると、いずれも?と首をかしげてしまいそうです。
「安全」とは一体どういうことなのでしょうか?
国際的な安全の定義については2014年、ISO/IEC GUIDE 51:2014で「許容できないリスクがないこと」と定義されています。

つまり、「絶対安全」ということはなく常にリスクは存在しているが、それが許容できる範囲なら「安全」として考えよう、といった意味です。確かにこう考えると、『リスクとは』の章に出てきた「包丁」についても当てはまるような気がします。
「たまに指を切ることもあるが、それほどたびたびでもないし、大けがをするほどでもないので、この程度なら(得られる利益・利便と比較して)それほど大きな危険はない(≒安全)と考えて使ってもいいだろう」、といった意味合いになります。
こういった考え方によると、安全化とは「リスクを許容限度以下に抑えること」になります。
従って、「リスクの大きさ」がわかれば「許容限度」と比較して、それを超えるものについて対策を講じていけば安全化につながることになります。
ただし、ここに一つの疑問があります。それは「許容限度」には基準があるのか?ということです。例えば脚立から転落することを想定し、その可能性やけがの程度には国際的な基準や、公的な基準があるのかということです。
答えは今のところ「ノー」です。(将来的にはわかりませんが)「許容限度」だけではなく、「可能性の度合い」や「重篤度」の見積り基準、あるいはそれらによって判定するリスクの大きさについての基準もありません。
リスクアセスメントはあくまで自主的な安全活動です。法令違反となる場合を除き、どういう基準を作って運用するかは個々の事業者に任されています。例えば、ある事業者にとって「受け入れられないリスク」という判定であったとしても、他の事業者に適用するものではないということです。
スーパーマーケットで10kgの荷物を持ち上げ移動することが「受け入れられないリスク」と判定されたとしても、同じことを建設業の事業者で「受け入れられないリスク」と判定するかどうかは不明です。なぜなら対象となる集団の構成メンバー(性別・年齢などの違い)や作業頻度も変わってくるからです。
このように、「リスク」についての判断は人や集団によっても違ってくるということを踏まえたうえで、各事業者・各職場に適した基準を作りリスクアセスメントを実施して戴きたいと思います。
実際リスクを低減するにあたっては、ある程度のリスクは残ること(これを「残留リスク」といいます)を容認して、「許容可能なリスク」にまで低減する対策を立てます。したがって、絶対安全ではありません。また、さらなる安全を目指し、広く受け入れ可能なリスクにまで低減することに努めなければいけません。
リスクアセスメントとは
リスクアセスメントとは?
「リスク」に「アセスメント」がついていますが、アセスメントとは
- 調査
- 事前影響調査
- 評価
- 査定
といった意味があります。
ですから、リスクアセスメントとは「リスクの調査・評価」といった意味合いになります。なお、現在労働安全衛生の分野(企業や現場など)で使われている「リスクアセスメント」という用語は、これに加えて「調査の結果による対策・改善措置」も含まれて使用されているのが一般的です。
従って、職場で扱うリスクアセスメントとは、『業務のうえで「負傷又は疾病が発生する可能性」があることがらについて、その「可能性の程度」と、万一発生した場合の「負傷又は疾病の重篤度」を見積もってリスクの大きさを評価し、必要な場合は対策を検討して実施すること』、といった意味になります。
つまりリスクアセスメントとは、事故災害を未然に防止する目的でリスクを事前に評価して対策をたて実施する手法です。
具体的には、①危険性又は有害性を特定し、②リスクを見積って、リスクを優先順位づけし、③リスクの低減措置を検討し、④リスク低減措置を実施することを体系的に進めます。(労働安全衛生法第28条の2)
労働安全衛生法では、リスクアセスメントを「危険性又は有害性等の調査」と表現し、リスクアセスメントの実施とその結果に基づくための必要な措置を「調査の結果に基づく措置」と表現していますが、以下本稿では、「リスクアセスメント」は、措置まで含めて話を進めます。
リスクアセスメントの説明動画
◆ リスクアセスメントは、なぜ必要なのでしょうか。
背景にある労働災害の現状と法的位置づけ、およびリスクアセスメントの効果をしっかりと認識しましょう。
なぜリスクアセスメント?① ~イギリスの取り組みと5ステップ方式~
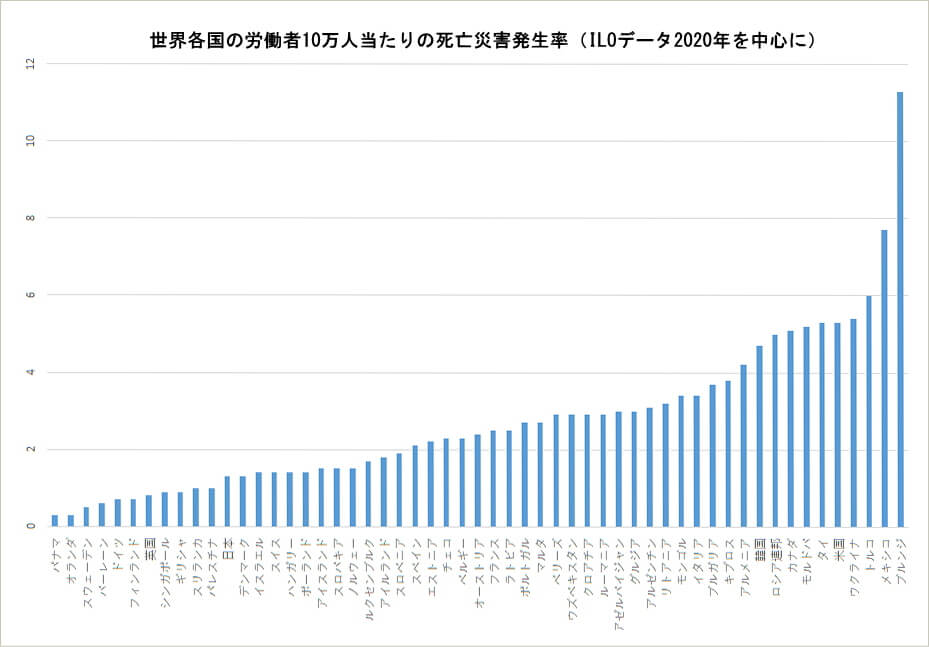
(注)メキシコ2021年、スイス2019年、英国2018年、米国2018年のデータ(資料出所:ILO 参照:中災防)
主要先進国の中で非常に労災死亡率が少ないのはイギリスですが、1974年にイギリスで労働安全衛生法が制定される際、専門委員会による『ローベンス報告』というのがあり、「安全衛生関係の法律が多すぎる」「行政機関も多くて複雑」「労災発生に応じて法律を次々作っても際限がない」など、それまでのやり方に対する反省・批判がなされました。それを受けて制定された法律はわずか84条で構成されています。
そして、法律を補うものとして進められた手法が、個々の企業の自主性に任せた「リスクアセスメント」だったのです。その結果、労災死亡率がとても低いと言われる国になっていったことから、日本でもこのことから学び、平成18年(2006年)に法制化されたという経緯があります。
つまり、基本的な法律は必要だが、それに加えて自主性的な活動が非常に大切だということが言えると思います。
また、イギリスでは誰でも簡単にリスクアセスメントを実施できるようにするため、手順をわかりやすい5つのステップにまとめることで実践率を向上させたそうです。
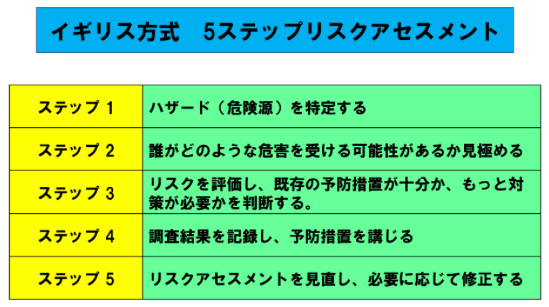
なぜリスクアセスメント?① ~イギリスの取り組みと5ステップ方式~
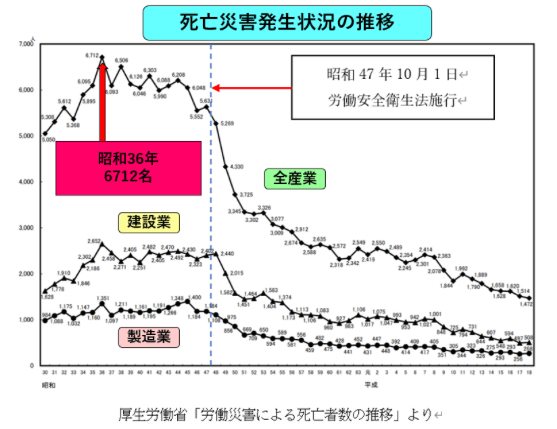
上の図は我が国の労災死亡者数のグラフですが、昭和47年(1972年)労働安全衛生法が制定される前と後を比べてみると、その違いに驚きます。もちろん、翌年(1973年)に起こった第1次オイルショックによる産業構造の変化や、公害問題など環境問題に対する社会全体の意識の変化なども影響していると思われますが、それらを差し引いても大変効果のあった法律と言われています。
ところで、この法令の中身はどうやって作られたのかというと、それ以前に起こった労働災害を分析し、そこから得られた内容を基にルール化したものと言えます。別の言い方をすると、
- 沢山起こったケースはルール化するが、レアなケースは除かれる
- 死亡災害や重症災害への対策はルール化するが、そうでなければルール化しにくい
- 広範な業種で起こることはルール化するが、特殊なケースなどはルール化しにくい
といったことが挙げられますが、社会全体に対し法令として制定するのですからやむを得ない面もあります。
これは国全体の基準であって守らなければならないが、国内全ての業務や労働環境をカバーするものとは限らず、法令を守っていれば災害が起きないとは言えないということがお分かりいただけると思います。
従って、リスクアセスメントは、安全衛生関係法令をカバーする自主的活動として必要不可欠なものと考えられます。
また、労働契約法(平成19年法律第128号)第5条では、以下の条文で使用者(事業者)の安全配慮義務を定めています。(労働者の安全への配慮)
第5条 使用者は、労働契約に伴い、労働者がその生命、身体等の安全を確保しつつ労働することができるよう、必要な配慮をするものとする。
「安全配慮義務」は昭和40年代から(1960年代後半~70年代前半)の労働災害を巡る損害賠償訴訟の結果、使用者側の契約上の義務のひとつとして判例が積み重ねられ、「対象者の安全や健康を左右できる立場にある者が、災害の予見可能性と回避可能性がある限り、講じられる手段を尽くす義務」として運用されてきた経緯があります。
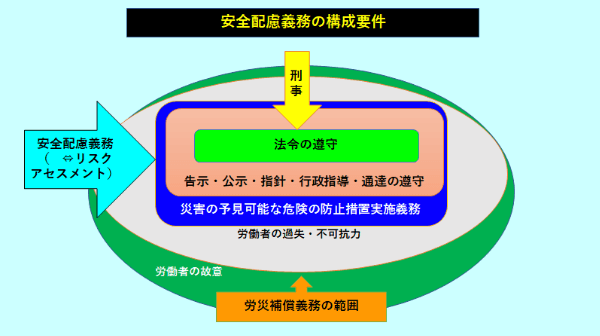
リスクアセスメントとは正に災害の発生を予測=予見し、結果を回避すべく対策を講ずることですから、安全配慮義務を実行する有効な手段としても適した手法と言えます。
労働災害の現状
我が国の労働災害による死亡者数は長期的に減少傾向にあり過去最小となりました。
しかし、休業4日以上の死傷者数は、近年、増加傾向にあり、3年連続で増加しています。
この背景として、設備の老朽化・大型化、高エネルギー化、工程の多様化・複雑化、混在作業の普及、熟練技能者の不足、技能の伝承不足があげられます。
こうした中、頭打ちにある労働災害件数を減少させるためには、経営者が積極的にリスクの取組に関与し、会社が一丸となって労働災害を未然に防止する活動、すなわちリスクアセスメントが必要となってきました。
法的位置づけ
労働安全衛生法により、リスクアセスメントに関する事項が規定されています。
(1) リスクアセスメント実施の義務化
①次の2つの事業者について、リスクアセスメントの実施が努力義務化されています。
(労働安全衛生法第28条の2、平成18年4月1日施行)
・化学物質等による労働者の危険又は健康障害を生ずるおそれがある事業場
・安全管理者の選任義務のある業種の事業場
②さらに、指定された化学物質(平成28年6月1日現在640種類~SDS交付義務もあり)の製造・取り扱う事業場に対して、リスクアセスメントの実施が義務化されました。
(労働安全衛生法第53条の3、平成28年6月1日施行)
(2) 安全委員会・衛生委員会の付議事項
安全委員会および衛生委員会の付議事項として、「リスクアセスメントの実施」が第2項に追加されています。
(労働安全衛生法第21条第2項、第22条第2項、平成18年4月1日施行)
(3) 総括安全衛生管理者の業務
総括安全衛生管理者の業務として、「リスクアセスメントの実施」が追加されています。
(労働安全衛生法第10条第5項、労働安全衛生規則第3条2第2項、平成18年4月1日施行)
(4) 安全管理者、衛生管理者の業務
安全管理者および衛生管理者の業務として、リスクアセスメントの実施が追加されています。
(労働安全衛生法第11条、第12条、平成18年4月1日施行)
(5) 安全管理者、職長教育の教育項目
安全管理者の選任に伴う研修や事業者責任とし実施しなければならない職長教育の教育項目にリスクアセスメントがある。
(労働安全衛生規則第5条、基発0224004号、労働安全衛生規則第40条、平成18年4月1日施行)
(6) 機械等の設置に伴う計画届の免除要件
事業者は、製造業等で定格容量300kW以上の建設物や機械等(仮設を除く。)を設置し、若しくは移転し、又はこれらの主要構造部分を変更しようとするときは、その計画を工事開始の 30 日前までに、労働基準監督署長に届け出なければなりませんが、その計画届の免除要件のひとつに、リスクアセスメントの実施があります。
(労働安全衛生法第88条、労働安全衛生規則第87条、平成18年4月1日施行)
◆ リスクアセスメントには、手法があります。
次の『5つのステップ』を順次実施してください。
ステップ1 危険性又は有害性の特定
ここでいう、「危険性又は有害性の特定」とは、特定した危険性又は有害性が「災害に至るまでのプロセス」を予測することをいいます。
したがって、「~するとき、~したので(危険性又は有害性に接近)、~になる(災害)」又は「~なので、~して(危険性又は有害性に接近)、~になる(災害)」と表現してください。
危険性又は有害性を特定するための情報源は、毎日の作業手順、ヒヤリハット活動、安全施工サイクル、安全パトロール、事故災害事例、安全目標の達成評価、前年度の災害発生状況などがありますので、それらを参考にするとよろしいかと思います。
ステップ2-1 リスクの見積もり
リスクには程度があって、リスクが大きいほど、負傷又は疾病の重篤度が高いか、発生する可能性が高いかのどちらかです。リスクの程度を知るには、リスクの程度を数値化してあげるとわかりやすいと思います。
高い数値ほど、リスクの程度は高いことになります。数値化する方法には、3段階法と4段階法がありますが、ここでは、簡潔な3段階法の加算式をとりあげます。
[負傷又は疾病の重篤度]
- 3—–死亡、極めて重大(永久的損傷、休業災害1か月以上、腕・足の切断、重症中毒)
- 2—–重大(休業災害1か月未満)
- 1—–軽微(不休災害やかすり傷)
[発生の可能性]
- 3—–確実又は可能性が極めて高い(よほど注意しないと負傷する又は疾病になる)
- 2—-可能性がある(注意していないと負傷する又は疾病になる)
- 1—-ほとんどない(注意していなくてもほとんど負傷しない又は疾病にならない)
[リスクの見積もり([負傷又は疾病の重篤度]+ [発生の可能性]と加算した数値)
- 6—-直ちに解決すべき問題がある
- 5—重大な問題がある
- 4—かなり問題がある
- 3—多少問題がある
- 2—問題は少ない
ステップ2-2 リスクの優先順位づけ
リスクを見積もった数値に対して、それぞれ優先順位をつけます。
- 見積もり6—優先度Ⅴ(即座に対策が必要)
- 見積もり5—優先度Ⅳ(速やかに対策が必要)
- 見積もり4—優先度Ⅲ(何らかの対策が必要)
- 見積もり3—優先度Ⅱ(必要に応じて対策する)
- 見積もり2—優先度Ⅰ(対策の必要なし)
ステップ3 リスク低減措置の検討
リスクの優先順位に従って、リスク低減措置を検討しますが、それにも決まった手順があります。すなわち、最初は、(1)本質的対策から検討してくださいということです。
ダメな場合は、順次(2)工学的対策、(3)管理的対策へと進み、最後に防御手段として(4)保護具の使用を検討するという手順です。
最初から、安易に保護具の使用の対策で終わりということがないように気をつけてください。
(1)本質的対策
最初に設計・計画段階で方法や設備を見直すことです、すなわち本質的対策を講ずることです。
例えば、リスクのある作業を見直し別の作業に変更するとか、設備を自動化して人の接触をなくしたりするとか、無害な材料に変更したりするとかです。
(2)工学的対策
防護柵を設置して人が接触しないように隔離すること(隔離の原則)、または安全装置を取り付けて人が近づいたら機械が停止するインターロックの設置(停止の原則)といった工学的対策を講ずることです。
(3)管理的対策
作業手順書や安全マニュアル(立入禁止の掲示も含む)で作業者に教育訓練するわけですが、作業者が正しく理解し、判断し、操作することで、不安全行動や不安全状態を取り除かれます。しかし、人は、ヒューマンエラーがつきまといますので、ヒューマンエラーの防止対策が必要となります。
(4)保護具の使用
(1)~(3)の対策でリスクを除去・低減できなかった場合の最後の手段として、保護帽、安全靴、保護衣、保護マスクといった保護具を使用することで、身を守ることを検討します。
ステップ4 リスク低減措置の実施
実施するリスク低減措置が決定したら、実施担当者がリスク低減措置を実施します。なお、リスク低減措置実施後には、特定された危険性又は有害性について、作業者の意見を求め、再度、リスクの見積りを行い、リスク低減措置の効果と作業性、生産性等に及ぼす影響を確認する必要があります。
また、措置後に新たな危険性又は有害性が生じていないかを確認することも大切です。 万が-、新たな危険性又は有害性が生じた場合には、実施したリスク除去・低減措置を再検討し、必要な措置を実施しなければなりません。
リスク低減措置を実施しても、技術上の問題などで、現状ではこれ以上リスクを低減できず、やむを得ず大きなリスクが残留してしまうことがあります。リスクが低減されていないものは、無理に下げずにそのままをリスクアセスメントの実施記録に記載し、その内容を作業者に周知させるとともに、必要な保護具の使用、安全な作業手順書の徹底を作業者に教育します。
ステップ5 リスク低減措置の記録と有効性の確認
リスクアセスメントを行い、リスク低減措置を実施したら、これですべて終了ではありません。
リスクアセスメントの結果を記録に残し、リスク低減措置が有効であったかを評価する必要があります。 効果があった低減措置は水平展開に活用できますし、効果がなかった低減措置は見直さなければいけません。
◆ 実際に、リスクアセスメントを実施してみましょう。
- アーク溶接作業
屋内の炭酸ガスアーク溶接作業ですが、近くに塗料や段ボールが置かれています。
ステップ1 危険性又は有害性の特定
- 溶接作業中に、発生するヒュームを常時吸って、じん肺になる。
- 溶接作業中に、発生するスパッタが飛散し、周囲の可燃物(塗料、段ボール等)に付着し火災・爆発し作業者が火傷する。
- 溶接作業中に、地震等の振動でボンベが転倒して作業者に当たり負傷する。
ステップ2 リスクの見積もりと優先度
- 重篤度3、発生の可能性2、見積もり5—–→Ⅳ(速やかに対応が必要)
- 重篤度3、発生の可能性3、見積もり6—-→Ⅴ(即座に対応が必要)
- 重篤度2、発生の可能性3、見積もり5—–→Ⅳ(速やかに対応が必要)
ステップ3 リスク低減措置の検討
- 局所排気装置の設置及び点検と防塵マスクの着用
→重篤度1、発生の可能性1、見積もり2-→Ⅰ - 周囲の可燃物を除去し、周囲に置かないようにする。
→重篤度1、発生の可能性1、見積もり2-→Ⅰ - ボンベを転倒防止用架台に設置し、二重チェーン掛けして固定する。
→重篤度1、発生の可能性1、見積もり2-→Ⅰ
- フォークリフト運搬作業
ボックスパレットのフォークリフト運搬作業ですが、前方に仕分け作業している作業者がいます。
ステップ1 危険性又は有害性の特定
- ボックスパレットを積みすぎて、前方の視野が見えないため、前方で作業していた人に突進し大けがを負わせる。
- ボックスパレットの高く積みすぎていたため、ボックスパレットが荷崩れて、前方で作業していた人に当たり負傷する。
- フォークリフトのパレットへの差し込みが浅かったため、ボックスパレットが荷崩れて、前方で作業していた人に当たり負傷する。
ステップ2 リスクの見積もりと優先度
- 重篤度3、発生の可能性3、見積もり6—–→Ⅴ(即座に対応が必要)
- 重篤度2、発生の可能性3、見積もり5—–→Ⅳ(速やかに対応が必要)
- 重篤度2、発生の可能性3、見積もり5—–→Ⅳ(速やかに対応が必要)
ステップ3 リスク低減措置の検討
- 前方の視野が見えない場合は、バック走行し、かつ速度を落とす。
→重篤度2、発生の可能性1、見積もり3–→Ⅱ(必要に応じて対応する) - ボックスパレットの高さは2段までとし、かつ荷崩れしないようにロープ掛けする。
→重篤度1、発生の可能性1、見積もり2-→Ⅰ - フォークをパレットの根本まで深く差し込み、かつ荷崩れしないようにロープ掛けする。
→重篤度1、発生の可能性1、見積もり2-→Ⅰ
◆ リスクアセスメントの歴史を見てみよう。
リスクアセスメントの成り立ち
本稿では主に労働安全衛生の範囲に限定して「リスクアセスメント」を扱っていますが、この章では少し視野を広げてリスクアセスメント全般について、その成り立ちや現状について概要を把握したうえで、改めて労働分野のリスクアセスメントを見てみたいと思います。
■言葉の意味について
リスクアセンスメントのキーワードとなる「Risk」はイタリア語のriscareに由来する言葉で、「勇気を持って試みる」という意味があったそうです。
古くは古代ギリシャ語の“ριζα(riza)”まで行き着く という説もあります。ホメーロスのオデュッセイアの話に由来し、「海上で避けることが難しいこと」や「断崖の狭間を巧みに船を操ること」を指す言葉になり、 その後大航海時代までに、イタリア語(risico、risco、rischio)、スペイン語(riesgo)、フランス語(risque) などに形を変えていき、大航海時代には「勇気をもって敢えて試みる」という意味で使われていたようです。
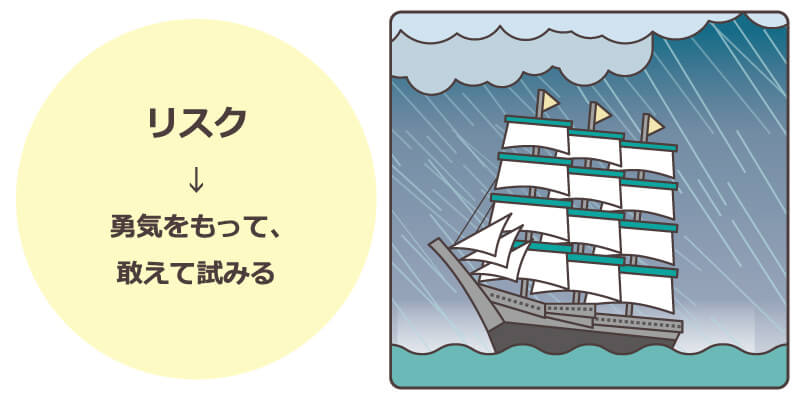
以上はいずれも「自ら選択して行動すること」がその意味に込められています。これがリスクの元々の意味であり、今でも例えば投資の世界などで「リスクを取る」といった表現があるように一部にそのニュアンスは残っているようです。
一方、大航海時代既に存在していた海上保険はその航海と同様多分に投機的なものだったのですが、やがて18世紀後半には統計データを前提とする損失発生の確立及び損失額の期待値を合理的に算出することで、近代的な保険事業として確立されていきました。この頃から保険業界での「リスク」という言葉は「損失発生の確立及び損失額の期待値」を示すようになりました。

保険会社と言えばすぐ思い出すのは有名な1:29:300の法則を唱えたハインリッヒ。1929年保険会社の技術・調査部の副部長の時、論文で唱えた法則が90年以上を経た今でも一定の評価を得ています。
さて、さらに現代に至って、リスク(Risk)という言葉は、次の代表的な例のようにいくつかの意味に使われています。
- ①「人やモノに 被害を与える事象」
- ②「損失の可能性」
- ③「損失の規模や大きさ」
- ④「特定の原因または要因による保険上の担保危険」
一般的な用法としては、上記①「人やものに被害を与える事象」が多く、② 「損失の可能性」及び③「損失の規模の大きさ」を含め、どちらかというとネガティブな意味で使われているという共通点はありますが、必ずしも一義的な意味で使用されてはいないようです。
それもそのはずで、今やリスク(アセスメント)は労働分野は勿論、社会学や経済学、法律学、工学、政治学、統計学、環境問題など様々な分野でテーマとされ、研究・実践されているのですから、その数だけ定義があると考えてもいいかもしれません。
■多様化するリスク
近・現代社会においてはリスクをどうとらえ、どう対応してきたのでしょうか?
例えば、ウルリッヒ・ベック(独)は1986年著書『危険社会』の中で、「近代産業社会が様々なリスクを生み出し、われわれの生命と社会関係をむしばむ時代を迎えるようになった」と主張し、「リスク社会の到来」を指摘しました。当時チェルノブイリ原発事故の直後だったこともあり、大きな反響を呼ぶとともに、「近代では生産活動に焦点が当てられるあまり負の側面を適切に処理してこなかった」、ということが大きな問題として提起されたのです。
確かに近代化によって人間は活動の自由を獲得してきましたが、それは人生の様々な場面での選択肢が増えたということでもあります。そのこと自体何だかとてもハッピーな事のようですが、好むと好まざるとにかかわらず数多くの選択を迫られるようになったという言い方もできるわけで、そうすると何だか少しネガティブなことのようにも思えます。 例えば江戸時代なら東京(江戸)から大阪(大坂)への移動手段は、基本的に徒歩しか無かったわけですが、今は飛行機もあれば新幹線もあり、自動車、自転車や昔ながらの徒歩旅行を試みるのも自由です。そしてそれぞれの選択に応じた多様なリスクが存在することも、容易に推測できると思います。
例えば、私たちは交通手段に関するリスクというとすぐ飛行機は意外と安全とか、新幹線は開業以来死亡事故ゼロだからとか事故発生率を考えがちですが、空港や駅までの道路が込んでいて乗り遅れることも、立派(?)なリスクです。あるいは、新幹線に乗る時にひょっとすると空席が無いかもしれないというのも、自由席選択によるリスクと言えるでしょう。また、台風の時期だと新幹線より飛行機の方がストップする恐れが高いとか、時間やお金に関係するリスクもあれば、交通機関のストライキなど多数に影響するリスクと持病など個人的な事情によるリスクなど、全くリスクという奴は多種多様です。

このように、産業社会の進展とともに生活の自由さや快適さを確保する欲求が高まるにつれ、皮肉なことにこれらを確保するため現代人は多くのリスクを背負わざるを得なくなりました。それに比例して社会全般のリスク意識も高まってきたという経緯があります。
結果的に現在、特に先進国においては人々の関心は成長・発展から安全・安心へと緩やかに移行するとともに、よりリスクに敏感な社会が形成されつつあると言えるでしょう。
では、実際の対応という面ではどうかというと、残念ながら「混沌としている」と言わざるを得ないようです。
「リスク」についての定義はそれぞれの分野で研究され、それなりに対応されています。例えば厚生労働省のWebサイトで「リスクアセスメント」を検索すれば、その目的や定義・一定のプロセスを知ることが出来ます。同様に経済産業省のサイトで「リスクアセスメント」を検索すると、こちらは主に製品安全に関する内容になっています。
このように、一定の指針なり方向性が示され成果を上げている分野もあるのですが、原発事故や森林破壊、地球温暖化、遺伝子操作、薬害といった、概ね20世紀後半以降に現れ始めたリスクは、その帰結の規模や深刻さを予見することが困難であり、国や個人ごとに相違する意見を調整し、どう対応するかという問題を突きつけられている状況です。
ブレア政権を支えたイギリスの社会学者アンソニー・ギデンズは、リスクを「自然的リスク」と「人為的リスク」の二つに定義づけて考察しています。
『近代とは生活と知の諸領域における合理化のプロセスにほかならず、それは行為の予見可能性をますます増大させるはずであった。ところが現在では、知識の増大や技術革新が予見可能性の確保に役立つどころか、むしろ逆に予見不可能性の増大をもたらしつつあるのではないか。原発問題など人間の知識や技術が産み出したリスクー「人の手で製造された不確実性 manufactured uncertainty」は、「それがリスクか否か」の認知や同定も含め再び人間の知識や技術に依存するといった再帰的な構造を有するとともに、個人生活、市場、地域共同体を超え地球全体を飲み込むグローバルな性格を持つことも見逃せない。』
何だか難しいことになってしまいましたが、このように様々な分野で研究・実践が行われているのが現状のようです。しかしながら包括的ないわばオールマイティーな「安全学」というものは、原発問題の決着や地球温暖化の阻止同様未だ確立されていません。
■労働分野のリスクアセスメント
そういった中で、リスクへの対応方法の制度化が比較的進んでいるものとして、労働分野のリスクアセスメントが挙げられます。
労働分野のリスクアセスメント制度の発祥は1982年のEC(欧州共同体、現EU)とされています。
とりわけイギリスでは、それ以前の1974年に現行の労働安全衛生法及び関連法規が制定されており、その基本的な理念は「事業活動によるリスクを生じさせた者が、あらゆる結果について労働者や一般市民の保護に責任をもつ」ということにありました。つまり、既にその時点で事業者は自主的なリスク対応を求められたという経緯があり、現在に至って主要先進国の中でも労災死亡者の発生率が一番低い国となっています。
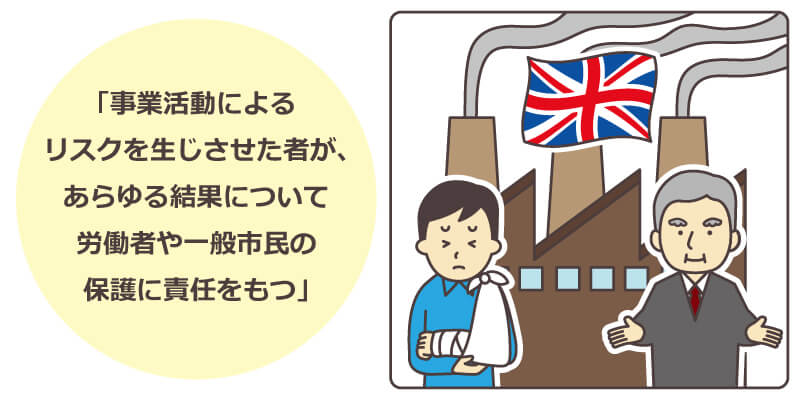
これらリスクアセスメントについて欧米が先行した背景には、以前から外国人労働者が多く、言語や習慣の違いから作業手順書などのマニュアルが重要視されていたことや、同じ理由で本質安全化が求められたことなどが挙げられます。
欧米では日本のようには安全教育に期待できないという背景もあり、労働者の行動を同一基準でコントロールしていくことが難しいという環境が、施設や機械設備の安全化という考え方を生み(本質安全化)、その過程で「リスク」という概念を「安全基準」に適用したと考えられます。
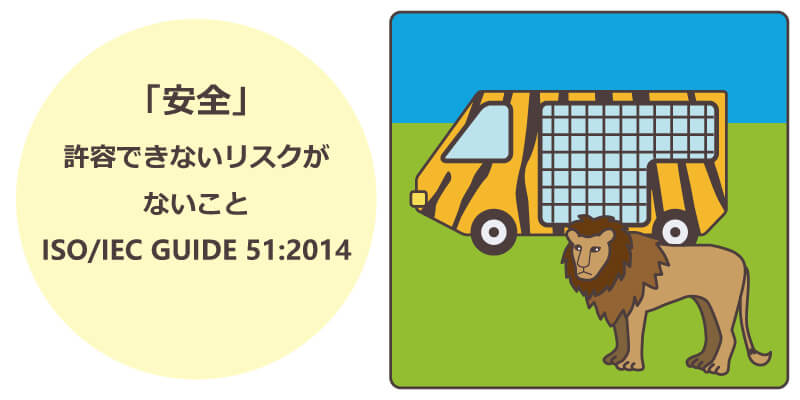
労働安全衛生の分野でよく言われる次のことは、前述の経緯をみるとなるほどと頷けるものがあります。
日本の安全の考え方
- 安全管理を徹底すれば災害は防止できる。
- 作業員の不安全行動が災害の原因。安全教育の徹底が必要。
欧米の安全の考え方
- 安全管理を徹底しても、災害そのものは防止できない。
- 作業員の不安全行動があっても重大な災害にならないように設備の本質安全化が必要
また、次の統計を見ると日本とリスクアセスメント先進国イギリスとの差に、考え方・取組み方の違いが如実に現れているようです。

すなわち、イギリスは災害発生率は日本ほど低くはないものの、死亡率は非常に低い数値を示しており、リスクアセスメントを通して「受け入れられないリスクの排除」を目指す安全化が一定の成果を挙げていると言えるでしょう。
KY活動や4S活動といった日本独自の手法を実践している多くの労働者や現場責任者、細かな法規制と指導で労災防止の実績を上げてきた行政組織と事業者といった、いわば「日本流のやり方」もまた災害発生率の減少には大変効果があったと言えますので、その上にリスクアセスメントの意味・目的を認識し、正しく実践していくことで「産業安全世界一」を実現できる日も近いと思うのです。
■まとめ
最後に、以上のことから導かれることを考察してみたいと思います。
・リスクアセスメントは必ずしも災害防止を目指していない。
少しでも労働分野に携わっている人が見るとギョっとするような言葉かもしれませんが、リスクアセスメントとは事業者のリスク管理の意思決定のため必要な調査・評価を行うことであって、労災防止を直接の目的としているわけではありません。
このことは前述のイギリス法の基本的な理念を踏襲したものと言えますが、日本の取り組みにおいて、ややもするとこの点を見落としがちかと思います。

安全の定義は「許容できないリスクがないこと」であって、必ずしも「リスクゼロ」の状態を指してはいません。リスクは無いに越したことはないがあってもよい、あってもよいが受け入れられないリスクはダメだ、ということです。するとその境目(基準)をどう判断するかということになりますが、本来リスクは未だ何も起こっていない段階でのものですから当然不確かなものです。この不確かなものを出来るだけ定量化し比較できるようにすることが、リスク管理の上で非常に重要なわけであり、その手段・手法が「リスクアセスメント」の中身というわけです。
そして、冒頭の「リスク」という言葉の変遷の中に「自ら選択して行動すること」という意味がかつてあったことを書きましたが、正に(事業者が)選択して行動する手段・手法としてのリスクアセスメントといった考え方です。 勿論、リスクに直接接する機会の多い、現場により近い人たちの意見や協力が欠かせないことは言うまでもありません。 各事業場の推進役となる方も必要不可欠ですので、より多くの方々に具体的な実施方法などを学んで頂き、実践を重ね成果を挙げて頂きたいと思います。

◆ リスクアセスメントを進める上で確認しておきたいページです。
リスクアセスメント関連のWebサイトをご紹介します。
法令・指針・通達・ガイドライン
安全衛生関係の法令は、安全衛生情報センター(https://www.jaish.gr.jp/)が見やすいと思います。
このほか政府や厚生労働省のWebサイトから検索することもできます。
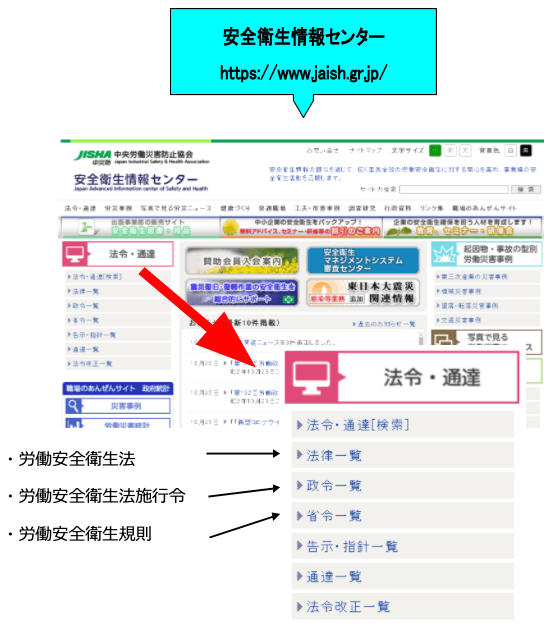

また、リスクアセスメントの具体的な進め方について、厚生労働省が示している三つの指針があります。
1.一般的なリスクアセスメントに関する指針(労働安全衛生法施行令第2条第1号及び2号の業種が対象)
・危険性又は有害性等の調査等に関する指針
https://www.jaish.gr.jp/horei/hor1-1/hor1-1-56-1-2.html
・危険性又は有害性等の調査等に関する指針について
https://www.jaish.gr.jp/anzen/hor/hombun/hor1-47/hor1-47-5-1-0.htm
・危険性又は有害性等の調査等に関する指針・同解説
https://www.mhlw.go.jp/bunya/roudoukijun/anzeneisei14/dl/ka060320001b.pdf
2.機械の製造者・使用者に対する指針(労働安全衛生法施行令第2条第1号及び2号の業種が対象)
・機械の包括的な安全基準に関する指針
https://www.jaish.gr.jp/horei/hor1-48/hor1-48-36-1-4.html
・「機械の包括的な安全基準に関する指針」の解説等について
https://www.jaish.gr.jp/anzen/hor/hombun/hor1-48/hor1-48-37-1-0.htm
3.対象となる化学物質を取り扱う事業者に対する指針(全業種が対象)
・化学物質等による危険性又は有害性等の調査等に関する指針
https://www.jaish.gr.jp/anzen/hor/hombun/hor1-14/hor1-14-6-1-0.htm
・化学物質等による危険性又は有害性等の調査等に関する指針について
https://www.jaish.gr.jp/anzen/hor/hombun/hor1-56/hor1-56-41-1-0.htm

合わせて読みたいページ
リスクアセスメントを学ぶ職長教育の対象業種は6業種に限られているため、研修用テキストが作成されています。
「リスクアセスメント担当者養成研修受講者用テキスト」
https://www.mhlw.go.jp/bunya/roudoukijun/anzeneisei14/130624-1.html
「リスクアセスメント担当者養成研修講師用テキスト」
https://www.mhlw.go.jp/bunya/roudoukijun/anzeneisei14/130624-2.html
機械を使用する事業者向けの指針をより具体的に解説したテキストです。
「機械ユーザー向け機械災害予防セミナー」
https://www.mhlw.go.jp/bunya/roudoukijun/anzeneisei14/dl/120501_2.pdf
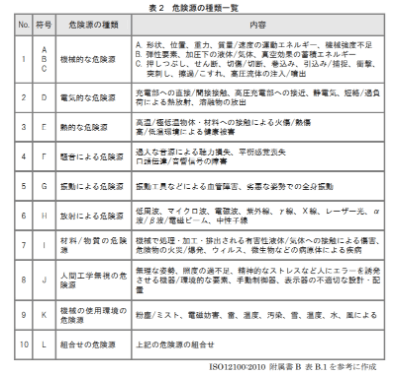
また、以下の例のように各種の作業別リスクアセスメント資料も作成されています。
「食品加工作業におけるリスクアセスメント」(リーフレット)
https://www.mhlw.go.jp/bunya/roudoukijun/anzeneisei14/dl/110713-00.pdf

「木材加工作業におけるリスクアセスメントのすすめ方」
https://www.mhlw.go.jp/bunya/roudoukijun/anzeneisei14/dl/080301b.pdf
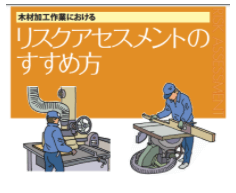
「運輸業等における荷役災害のリスクアセスメントのすすめ方」(リーフレット)
https://www.mhlw.go.jp/bunya/roudoukijun/anzeneisei14/dl/unyu1.pdf

以上は一例です。
実践に際して参考となる資料などは、厚労省Webサイトのトップページで「リスクアセスメント」を検索します。
https://www.mhlw.go.jp/index.html


沢山の資料がありますので、ご自分の業種・作業などに合ったものを選びダウンロードしてご使用ください。

受講者様のご希望に合わせ、以下のタイプの講習会もご用意しています




このページをシェアする
講習会をお探しですか?